Watch & Work: How Collaborative Robotics and Smart Sensing Are Transforming Industrial Polishing
Polishing industrial parts has traditionally been one of the most challenging tasks on the factory floor—demanding significant manual effort, exposing operators to health risks, and proving notoriously difficult to automate. Parts affected by wear, deformation, or manufacturing variances rarely match their original CAD models, making standard automation unreliable.
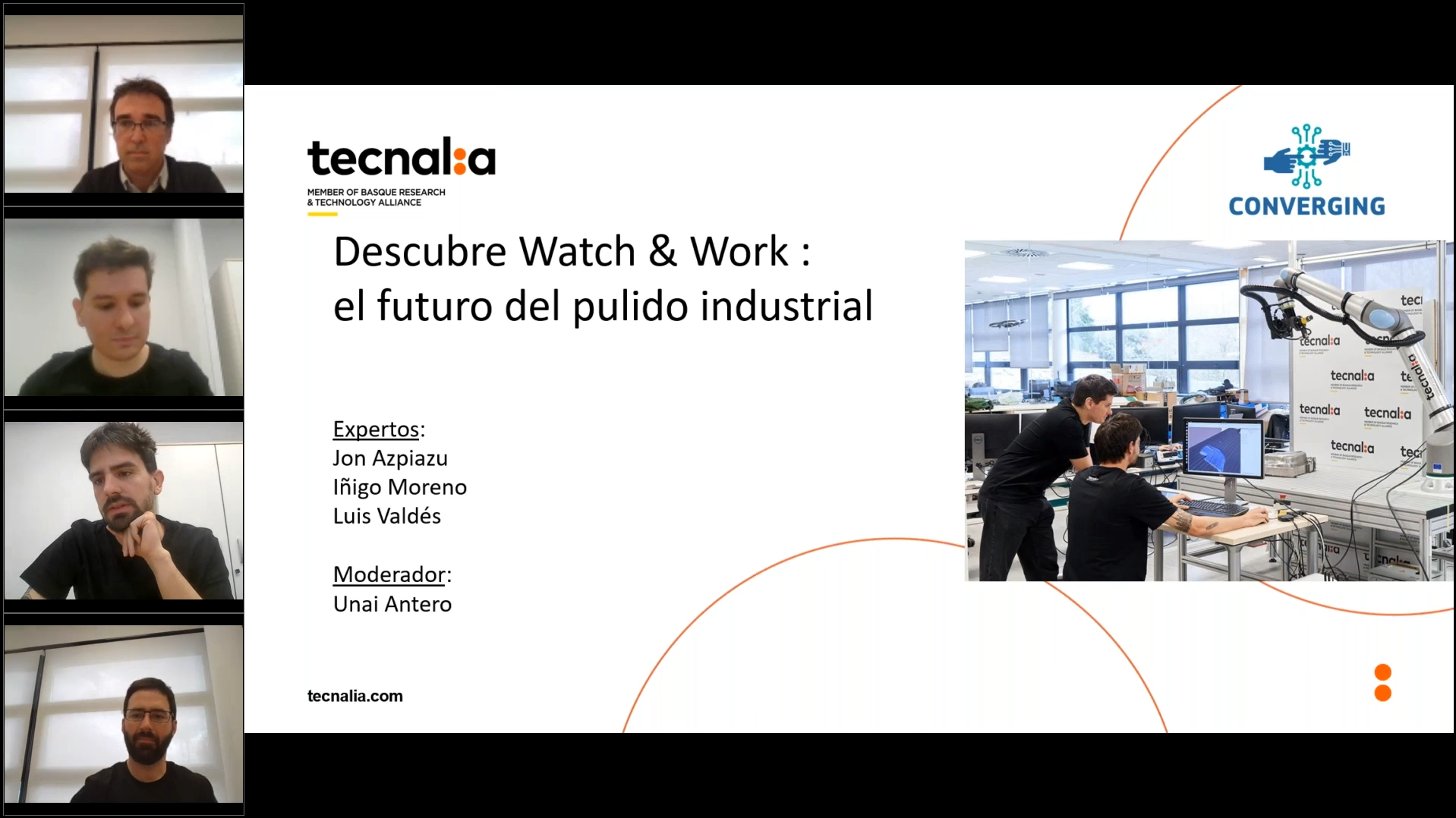
However, a new solution is changing the game. Developed under the CONVERGING initiative, Watch & Work combines high-precision sensors with collaborative robotics to deliver an intelligent, flexible, and safe approach to polishing and finishing tasks. In a recent webinar, experts behind the project showcased how this technology is reshaping industrial automation—and why it's poised to have a major impact across multiple sectors.
A Solution Born for Real-World Complexity
Watch&Work directly addresses the core challenges of traditional polishing processes:
-
Operator strain and exposure to vibrations, dust, and abrasives
-
Inconsistent quality caused by manual variability
-
Difficulties in programming robots to adapt to non-standard parts
At the heart of the solution is an intelligent system capable of reconstructing its working environment in real time. Using advanced sensors, Watch & Work scans each part—regardless of deformation or wear—and automatically generates optimized polishing paths. This capability eliminates the need for CAD-perfect models and enables true barrier-free automation.
Simplicity Meets Sophistication
One of Watch&Work’s standout features is its intuitive interface. Designed with usability in mind, it allows non-experts to operate the system with minimal training. Operators can easily define areas for polishing and adjust process parameters through a user-friendly control panel, eliminating the need for complex programming.
Additionally, force sensors integrated into the robotic arm ensure that optimal and consistent pressure is applied during the polishing process. The result? Smooth, flawless surfaces with repeatable quality—regardless of part condition.
Designed for Safety, Built for Flexibility
Safety is another key pillar of the Watch&Work system. By relying on collaborative robots (cobots), the technology ensures that humans and machines can work in close proximity without risk. The robots are designed to halt movement in case of contact, dramatically reducing the likelihood of accidents.
Flexibility is also built into the system. Watch&Work can be integrated with mobile robotic platforms, allowing it to move around large components and work without spatial constraints. This makes it an excellent fit for applications involving oversized or complex parts—such as those found in the aerospace, metallurgy, or automotive industries.
Broader Applications and Measurable Benefits
Beyond polishing, Watch & Work’s adaptive approach lends itself to a wide array of finishing operations—including painting, welding, and sanding. Its benefits span several dimensions:
-
Higher and more consistent surface quality
-
Quantifiable defect detection for quality control
-
Reduced labor costs by minimizing manual effort
-
Improved safety and reduced exposure to hazardous conditions
-
Adaptability to parts with wear, burrs, deformation, or manufacturing variability
Whether applied to high-end woodworking or heavy industry, Watch&Work enables adaptive programming that meets the needs of modern, dynamic production environments.
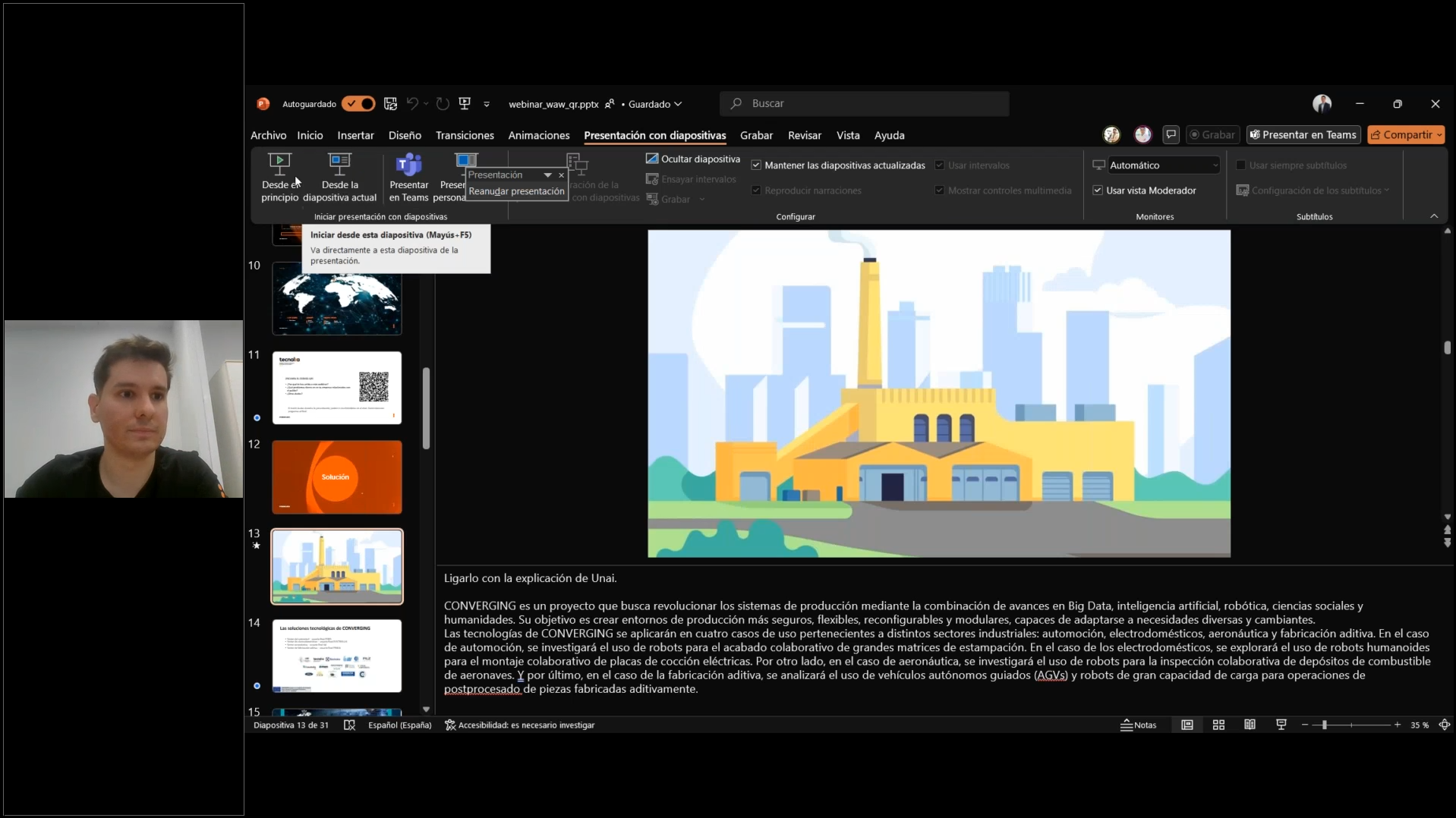
Managing the Transition: From Concept to Reality
Of course, introducing an advanced system like Watch&Work involves overcoming key challenges—such as integrating with existing workflows and upskilling personnel. These issues were also addressed during the webinar, with the project team offering insights into best practices for implementation and strategies for maximizing ROI in automation projects.
Expert Insights from the Webinar
The session featured contributions from:
-
Luis Valdes
-
Jon Azpiazu
-
Iñigo Moreno
Moderated by Unai Antero, the webinar provided technical demonstrations, use-case scenarios, and a deep dive into the underlying technologies driving Watch&Work forward.
A Glimpse Into the Future of Smart Manufacturing
As industries continue to evolve toward smarter, safer, and more adaptive production lines, solutions like Watch&Work are setting a new standard. Tackling one of the most demanding and hazardous industrial processes with a fresh, sensor-driven approach, it exemplifies the kind of innovation that the CONVERGING project is all about.
📺 To see Watch&Work in action and explore its full potential, you can watch the webinar recording below